The supply chain system was not really a different story before the pandemic came along. Rather, we became more aware of this complex order and how it functions, its inadequacies and flaws during that time. The lockdowns brought light to the intricacies and interdependence of each step of the chain, which would have been considered a great feat at the peak of globalization, but now simply mean that the global supply chain management is incompetent to match the dynamism of patterns of consumer demand.
Why did the supply chain crack?
Supply chain management is a global network through which goods and services flow, all the way from the stages of production, manufacturing, transportation, and finally, distribution to the end customer. It appears to be a linear process but is actually a complex web of multiple chains colliding and coinciding, creating networks that are extremely entangled.
It was due to this complexity that when the COVID-19 pandemic hit, lockdowns caused shutting down of different parts of the supply chain. Even though these lockdowns were temporary, they produced unimaginable delays and disruptions. A delay from one manufacturing unit meant that the next unit would be waiting to receive its intermediate goods, and a cascading effect followed. Backlogs were created and eventually hit the end customers, who had to wait weeks or months to receive their orders. The logistics industry was made aware of how incompetent the global supply chain management system is, that any natural calamity, pandemic or geopolitical instability can put a complete halt to this network.
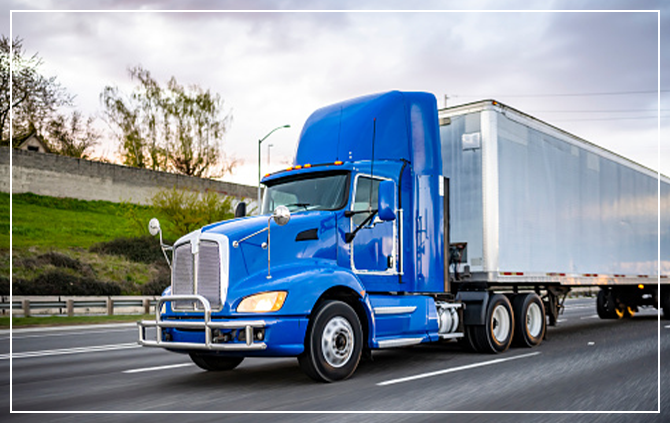
Trends that have emerged in supply chain management to close these gaps.
Supply chain risk has emerged mainly due to how international the process is. The interconnectedness has made it such that one little glitch anywhere along the chain can cause massive delays and cost concerns. Therefore, the major supply chain solutions that have come about to fix these issues are related primarily to locational changes. This means shifting manufacturing closer to home and redesigning the global supply chain management structures in search of sustainable solutions.
Wall Street Journal has recognized the following trends coming about to ease the bottlenecks in global supply chain management:
- Regionalization
Supply chains are spread and wide. Companies are now considering a new method called "regionalization" whereby they will set up industries in different parts of the world, which will supply to the stores in their region only. Doing this would minimize the risk of delays in shipping and transportation of products over longer distances, also cutting some of the costs involved. - Nearshoring
Hereby, companies are looking to bring their manufacturing units closer to home, where their major market exists. For instance, a French company whose major consumer group lies in Europe, would prefer to set up industries in countries around the Mediterranean Sea or the Balkan nations, instead of Asia. The opportunity cost would be the cheap labor available in Asian countries and easier trade routes to gather raw materials. - Reshoring
Taking nearshoring one step ahead, some enterprises plan to bring their entire manufacturing systems back to their home countries. All the production would be within the domestic boundaries, so that any problem during the different stages of production can be addressed timely to avoid or minimize delays.
However, it must be noted that these solutions are not a panacea. They themselves are riddled with problems – they are not guaranteed to be risk-free or inexpensive. There is the concern of high labor costs, extensive capital investments, adherence to global alliances for green technology, and many more. According to a 2020 report of Bank of America via the US-China Economic and Security Review Commission, the total combined cost for US and European companies to move manufacturing out of China would come around to $1 trillion over the next 5 years.
The costs of these changes are high, but the need to reduce supply chain risks and make them resilient for any future obstacles is much more critical.
Useful strategies for a resilient supply chain.
The changing patterns of supply chain management have put business enterprises on the edge of their seats. With this dynamism comes a need to keep up your business strategies fluid and open to improvement, so that any change can be addressed easily and effectively. Not all such strategies have to be expensive or radical, but little differences along the path can help in making supply chains more resilient.
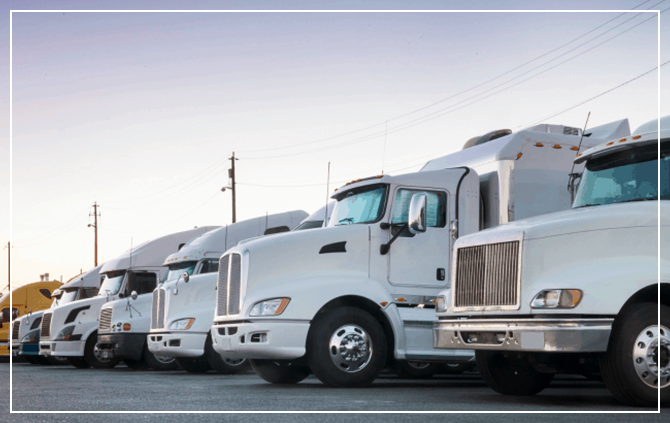
- Diversifying and sharing risks for low-probability, high-impact events.
- Building inventories at each step so that when there is a shortage, this buffer can be tapped into and the next unit in the chain isn't left waiting.
- Optimizing human capital to find and retain talent, and utilize HR management to correct any problems encountered.
- Supply chain visibility by making it possible to track every raw material, component or product in transit, right from the back-end to the final customer.
- Integrating IT and rethinking digital strategy in supply chain operations for better business intelligence, increased visibility and automating different aspects of supply chain management.
- Diversifying supplier base so that when one supplier runs out of materials you may need, you can contact another supplier for your requirements.
- Manufacturer's awareness about the other customers of their suppliers, so that any overlap or shortage can be looked into timely.
Transparency, sustainability and visibility - the knights of supply chain management.
A resilient supply chain is one that integrates transparency, sustainability and visibility to make the process simpler to understand, easily locate and address bottlenecks, and bring accountability to the logistics industry. Data has to be made readily available to all the stakeholders, and contingency plans set in place.
The current state of the supply chain is fixable, but the solutions have to be advanced from the traditional ones. Simple changes ought to be transformed into radical modifications.
After all, you and I wouldn't like to hoard toilet paper again, would we?